Grate Cooler Modification Technology
We present a unique and practical solution according to universal defect and non-avoided technical bottleneck in the use of grate cooler. On the basis of good cooling effect, our technology improve the thermal efficiency and operation reliability, and reducing the consumption of wearing parts, and make the maintenance and replacement of wearing parts more convenient, which greatly shorten the repair time.
1¡¢Owned intellectual property (ZL2011 20237738.1) "air self-adjusting grate plate beam"
2¡¢New type low consumption and high efficiency grate plate
3¡¢New type low consumption blind plate
4¡¢New type shaft seal
5¡¢New type material discharging system
6¡¢To solve the problems of shaft
7¡¢New type wall sealing device
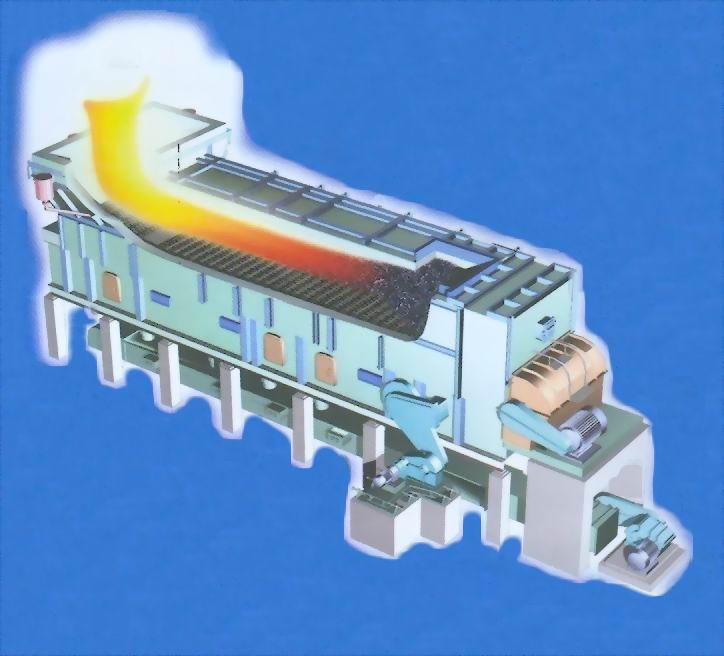
New Type Sealing Device for Rotary Kiln
We develop a flexible seal device which can be able to adapt to kiln body deformation, kiln body beat and decentration when rotary kiln is under the state of high temperature, because all sealing materials are high-temperature and made by special heat treatment process, so it can still maintain good mechanical properties at the kiln head temperature up to 1000 ¡æ ~1200 ¡æ, so as to ensure the sealing effect. The method is completely solved ash and air leakage problem caused by positive pressure, increasing tertiary air temperature on kiln head to ensure the normal thermal environment.
The technology has advantage of long service life, low cost, free maintenance, reliable operation, good sealing effect, easy installation and short construction period.
Technical Parameter
|
Labyrinth |
Graphite block
|
Spring pressure plate |
Cylinder pushing friction plate
|
Stainless steel scale
|
New type flexible |
Sealability
Air leakage factor
|
Worst
25%
|
Bad
15%
|
Worse
15%
|
Bad
18%
|
Normal
12%
|
Good
1%
|
Air and material leakage
High-temp. resistance
|
Critical
Bad
|
Critical
Bad
|
More critical
Bad
|
Critical
Worse
|
Critical
Normal
|
Non-leakage
Good
|
Fit clearance
Repair frequent
|
Big
Regular
|
Big
regular
|
Big
regular
|
Big
regular
|
Big
Normal
|
No
no
|
Difficulty for replace
Working life
|
Difficult
Long
|
Difficult
3months
|
Difficult
1 year
|
Difficult
6months
|
Easy
5months
|
Easier
3years
|
Operation reliability
kiln deformation adaptability
|
Reliable
Good
|
Bad
Worst
|
Bad
Worse
|
Non-reliable
Bad
|
Normal
Good
|
Reliable
Good
|
Comprehensive cost
Energy-saving
|
Low
worst
|
Higher
worse
|
Higher
Bad
|
High
Bad
|
Low
Normal
|
Low
Good
|
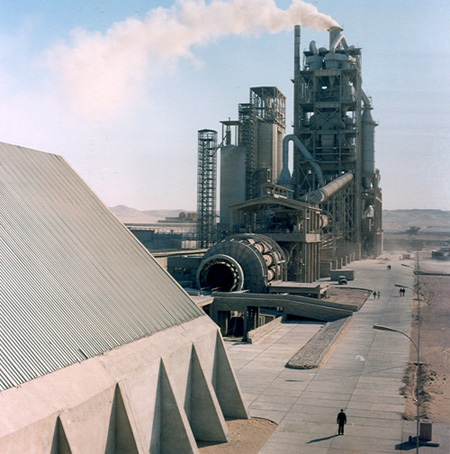
Mill Modification for Energy-saving
1. According to the mechanism of more crushing and less grinding, crushing unit consumption is lower than ball milling consumption, crushing machine is used before grinding, greatly reduce the mill feed size, balls are greatly smaller, which increase the mill output and reduce the power consumption of grinding;
2. Optimizing design and reasonable selection of grinding parameter;
3. Sieving compartment device is used inside mill which improve the opening rate.
4. The active liners are used inside fineness mill chamber which change the grinding body trajectory to eliminate "grinding body sluggish", to improve the efficiency of grinding.
5. Wear mechanism is different of mill lining plate according to the different parts, and use different strength, hardness and impact toughness, which can match the material and grinding media, to achieve high hardness, impact resistance, long service life, and remarkable energy saving effect.
6. High-quality grinding media (smooth surface, high hardness, low wear, good accuracy, stability and reasonable gradation) are selected, which can reduce the consumption of metal.
7. Metal remover must be set before mill and mill outlet which will reduce wear, improve the quality of the products.
8. High quality grinding aid (excellent dispersion properties, eliminate grinding adhesion), must be used which can prevent particle aggregation, improving the material flow, so as to improve the efficiency and shorten the grinding time.
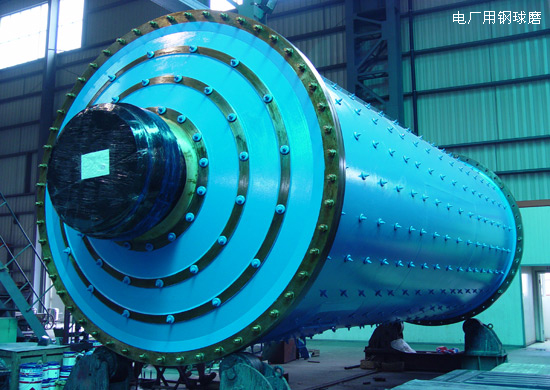
|